The housing crisis of 2007/8 is the very definition of the gift that keeps on giving.
A decade later we see that much of the country continues to find it’s mobility negatively affected by the housing crisis.
This is a surprising factor that is limiting growth in manufacturing jobs. In the past, if you were a worker in a Manufacturing plant with an advanced skill set and the plant closed, you could move to where the jobs are. But this assumes you can sell your house and move to a new location at will. Something that is impossible to do if you bought your home for — say $350K — and now find it is worth only $200K due to the housing crisis.
In other words, housing affects mobility which in turn affects the number of workers available to fill manufacturing jobs.
As reported by Deloitte and Manufacturing Institute (2011), there is a significant skill gap expected to result in a shortage of 2,000,000 skilled workers inside U.S. manufacturing plants:
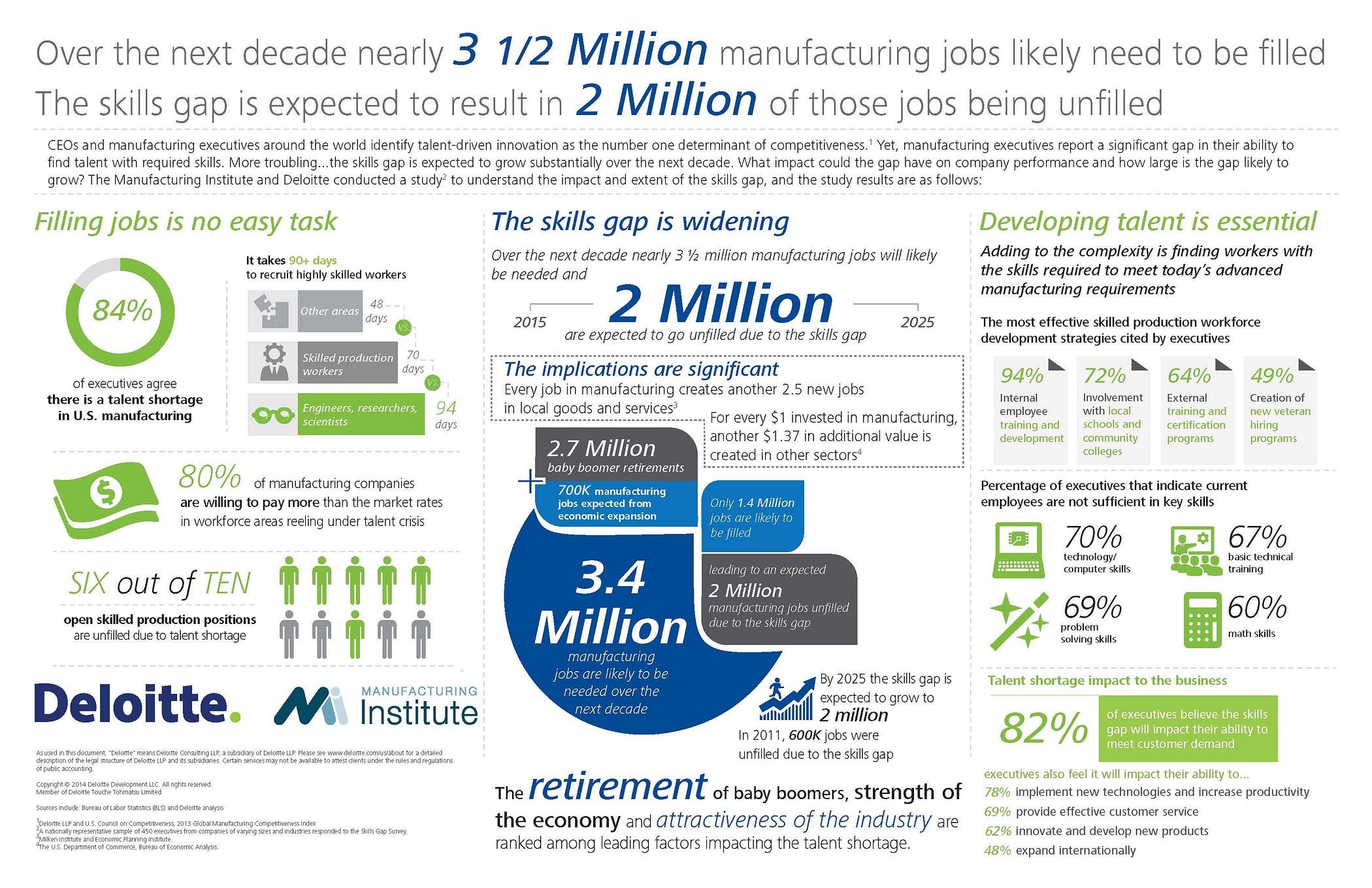
Overall, the housing crisis remains a widespread concern. Last summer’s MacArthur Foundation opinion survey found that 8 in 10 Americans felt that the housing crisis was still ongoing (MacArthur Foundation 2016).
A Three-Pronged Solution
There are three paths we think are worth exploring to solve the problem.
1. Focus on creating new manufacturing jobs in a metropolitan area, clustered around cities and research universities. That way, workers with the right skills need not sell their homes to move into new jobs as they get created in their community. Clustering around a few industry sectors builds a strong local ecosystem, one that can support a lifetime of work in the manufacturing sector.
2. Focus on creating a greater supply of workers with the skill sets our advanced manufacturing plants require. The skill sets tends to vary (a lot) by industry sector and/or employer. The Chicago school system is experimenting with aligning its high schools and community colleges with the explicit needs of high-growth industry sectors. For example, it has aligned the Crane High School, a school slated for closure, with the needs of the burgeoning medical field in Chicago. The resulting high school has been renamed the New Crane Medical Preparatory High School with a curriculum explicitly focused on creating graduates with the skill set needed to go into good paying jobs in the healthcare field. The high school works in concert with neighboring Malcolm X College.
3. Encourage workers to embrace lifelong learning. One of the reasons we like the Chicago example is that it encourages people to connect up with a local community college for ongoing education in their field. The pace of technology change has accelerated, making it imperative that even the most skilled workers focus on building skills in multiple areas, to maximize their ability to solve complex problems on behalf of advanced manufacturing concerns. Skills in particular demand include: prototyping, CAD/CAM, electronics, robotics, CNC tooling (lathes, routers).